Roller-Wave....What Is It?
In the mid-to-late '70's, I found that biasing the mixture to
the exhaust-side of the piston netted lower fuel consumption, as well as
considerably less tendency for detonation in 2-valve NASCAR and drag race
engines. Those experiments ultimately lead to swirl combustion technology that
dominates 2-valve race head design today. Today's 4-valve pent-roof combustion
chambers don't lend themselves to conventional swirl combustion as readily, so a
rethink was required to mechanically enhance their combustion properties.
Since confining mixture and initiating the burn on the
exhaust-side of the piston takes full advantage of exhaust-valve heat for
mixture ionization, I utilized tighter (and larger area) quench clearance on the
intake-side of the piston to force a mixture wave to flow toward the
exhaust-side of the chamber as the piston approaches TDC. I've incorporated less
piston dome volume on the exhaust-side with both more piston to head (quench)
clearance, as well as the trough that incorporates both exhaust valve relief's.
This trough lines up precisely with the down-sloping combustion chamber at TDC,
reflecting and rolling the mixture that's traveling toward it from the
intake-side. Confining a rolling turbulence to the exhaust-side of the piston
insures that more mixture components will be lighted during ignition, and a
faster, more complete combustion event will result....permitting one to use less
spark advance and fuel, to achieve more power and less detonation in any
application, whether normally-aspirated or forced-induction.
When one has the ability to shape the combustion event using
mechanical design, it's possible to also design the tuning parameters the engine
will "want", rather than living with compromised tuning and
performance created by the use of more generic combustion space designs.
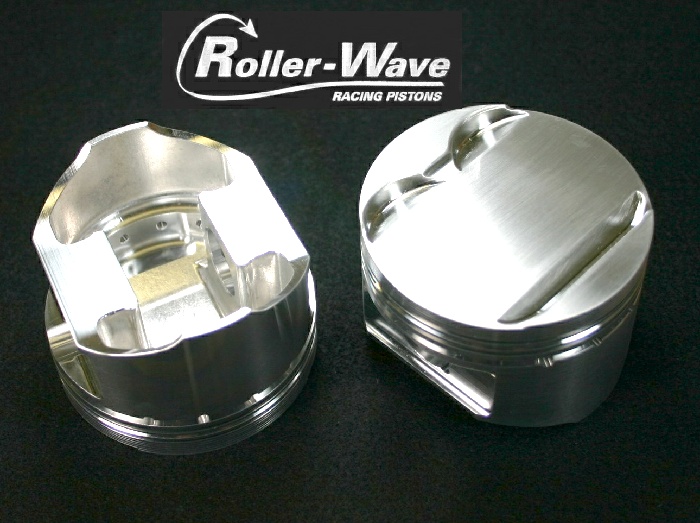
Roller-Wave forced induction pistons incorporate full
stepped-quench pads to maximize (mechanical octane), a volume-biasing reflector
trench on the exhaust-side, turbulators at the intersect of the valve relief's
to increase mixture homogeneity, and piston skirt designs for minimal cylinder
wall loading.
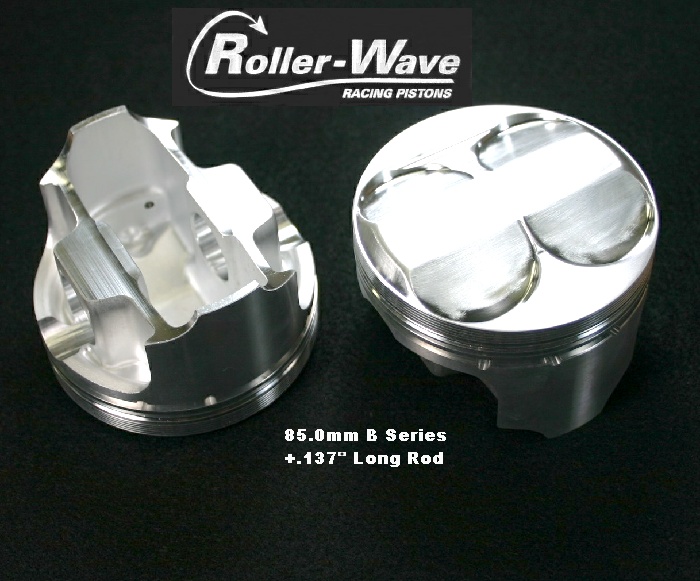
Many of our normally-aspirated B Series pistons incorporate
strutted-style skirts for significant weight savings. The mid-dome pistons
pictured above are favorites for large-bore VTEC applications restricted to
low-octane pump-gas.
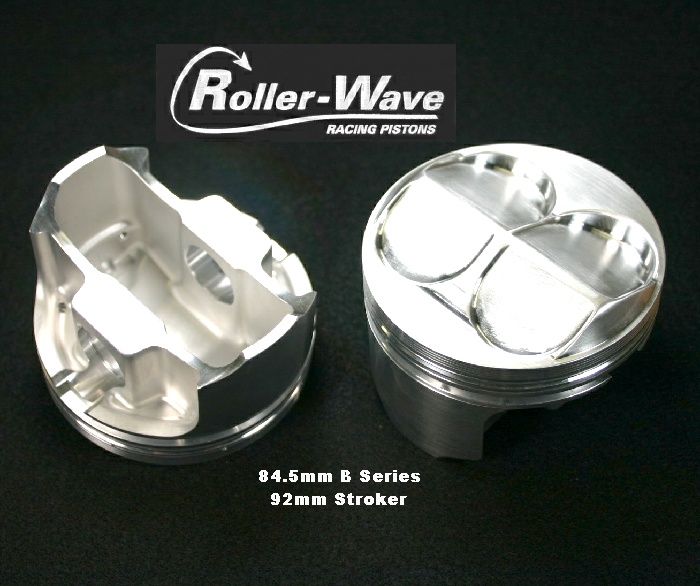
Another popular combination we stock consists of a 92mm Crower
crankshaft, our super-lightweight large bolt (long) Crower rods, and these high
compression pistons. These pistons incorporate lateral gas ports, groove-lock
spacers for oil ring support, and 8.50cc domes for maximum compression without
masking the flame front.
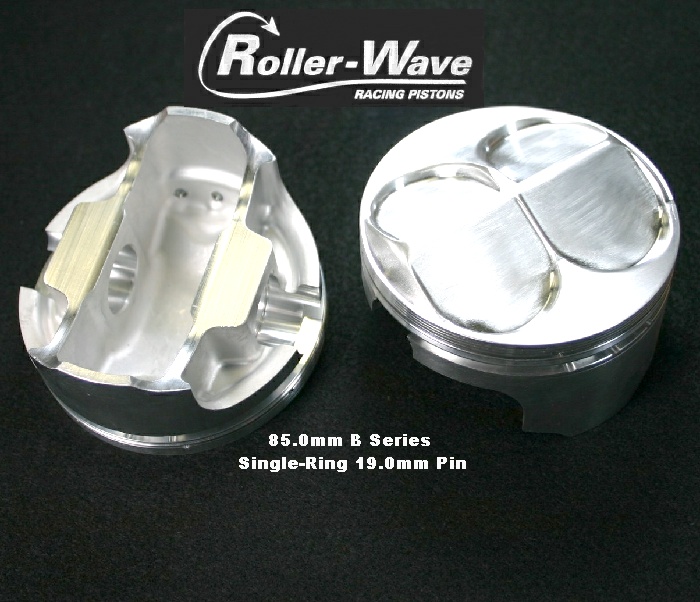
Road racers around the world run these Roller-Waves with
ultra-high 19mm pin placement for use with the longest-possible connecting rods.
Combined with 87.2mm stroke (ITR) cranks, these 85.0mm pistons net just below
2.0 liters. We stock both the pistons and the corresponding lightweight
Crower rods.
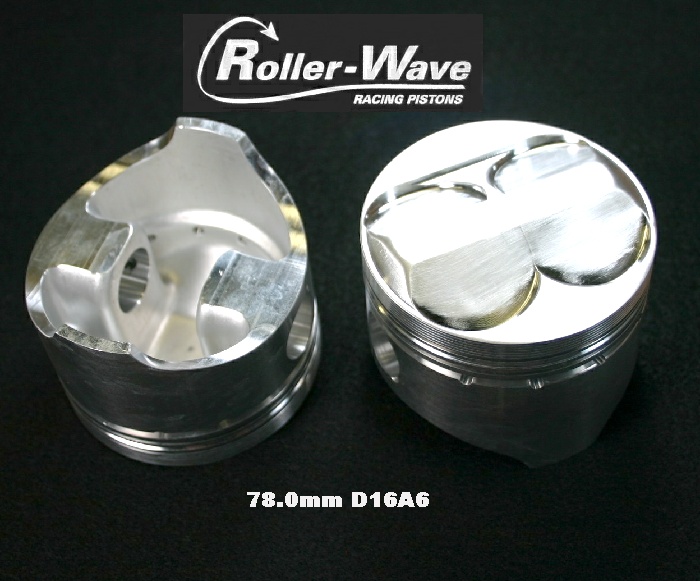
Sleeved D16 engine combinations are making a come-back these
days and we have a number of piston combinations designed expressly for them in
both NA and FI applications.
4G63-4G54
.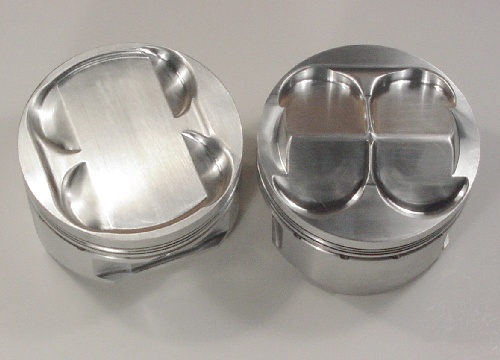
We've designed Roller-Wave pistons for the Toyota 2JZ turbo
applications running extreme boost pressure. They are available in stock,
+.5mm, and +.10mm oversize bore diameters. These pistons are also available
with Carrillo or Crower rods with relocated pins for two stroker
combinations.
Our Mini-Cooper Roller-Waves are available in stock or
oversize bore diameters. They are outfitted with custom Total-Seal rings
designed for these small-bore engines. We also stock Crower billet rods for
Mini's.
Our strutted-skirt Roller-Wave pistons for the Hyundai V-6 engines are
favorites for forced-induction applications.
Our FI and NA Volkswagen VR6 pistons provide higher static
compression than most other "generic" aftermarket pistons, netting
considerably more performance (off and on boost).